જેમ આપણે બધા જાણીએ છીએ, રોકાણ કાસ્ટિંગ ઉત્પાદન કરે છેકાસ્ટિંગચોકસાઇ ચોકસાઈ અને સારી પૂર્ણાહુતિ સાથે. જો કે, ની ઉત્પાદન પ્રક્રિયા દરમિયાનરોકાણ કાસ્ટિંગ, ત્યાં ઘણી સંભવિત સામાન્ય કાસ્ટિંગ ખામીઓ છે. અમારા એન્જિનિયરિંગ અનુભવ અને અદ્યતન સાધનોના આધારે, અમે કારણોનું વિશ્લેષણ કરીને આવી સમસ્યાઓને રોકવાનો માર્ગ શોધી શકીએ છીએ. નીચે, અમે ઘણી સામાન્ય કાસ્ટિંગ ખામીઓ અને તેના કારણો અને નિવારણ પદ્ધતિઓ રજૂ કરીએ છીએ. આશા છે કે આ લેખ અમારા ગ્રાહકોને સમસ્યાઓ સમજવામાં અને અમારા સહકાર્યકરોને મદદરૂપ થશે, આ વિશ્લેષણ તમને સંભવિત કાસ્ટિંગ ખામીઓને રોકવામાં મદદ કરી શકે છે.
અન્ડરકાસ્ટ અને ઠંડા અવરોધ
1. સમસ્યાનું વર્ણન:
અંડરકાસ્ટિંગમાં ઘણીવાર કાસ્ટિંગની પાતળી દિવાલમાં અથવા આંતરિક રનરથી દૂર સ્થાનિક રીતે માંસનો અભાવ હોય છે અને તેની ધાર ચાપ આકારની હોય છે. કોલ્ડ પાર્ટીશન એ છે કે પીગળેલી ધાતુની બે સેર સંપૂર્ણપણે ભળી નથી અને ત્યાં સ્પષ્ટ સાંધા છે.
2. કારણ:
1) નીચા પીગળેલા મેટલ રેડતા તાપમાન અને મોલ્ડ તાપમાન
2) રેડવાની ઝડપ ધીમી છે અથવા રનર સેટિંગ ગેરવાજબી છે, મેટલ ફ્લો ખૂબ લાંબો છે
3) કાસ્ટિંગની દિવાલની જાડાઈ ખૂબ પાતળી છે, અને પીગળેલી ધાતુનો પ્રવાહ નબળો છે
4) રેડતા દરમિયાન કાપી નાખો
3. નિવારક પગલાં:
1) પીગળેલી ધાતુ રેડતા તાપમાન અને મોલ્ડ તાપમાનમાં વધારો
2) પીગળેલી ધાતુના પ્રવાહને ઘટાડવા માટે રેડવાની ગતિ વધારવી અથવા આંતરિક દોડવીરની સંખ્યા અથવા વિસ્તાર વધારવો
3) રેડતા દરમિયાન કટ-ઓફ અટકાવવા માટે રેડતા રાઈઝરના દબાણના વડાને વધારો
સંકોચન
1. સમસ્યાનું વર્ણન:
તે માત્ર એક્સ-રે નિરીક્ષણ દ્વારા શોધી શકાય છે. સપાટીનું સંકોચન ફ્લોરોસેન્સ અથવા સ્ટેનિંગ નિરીક્ષણ દ્વારા શોધી શકાય છે. ગંભીર કિસ્સાઓમાં, તે રેતી ફૂંકાયા પછી મળી શકે છે.
2. કારણ:
1) કાસ્ટિંગ માળખું ગેરવાજબી છે, અને હોટ સ્પોટ ખૂબ વધારે અથવા ખૂબ મોટા છે
2) રેડતા રાઈઝરની ઉષ્મા ક્ષમતા નાની છે, જે ક્રમિક ઘનકરણ બનાવવામાં નિષ્ફળ જાય છે, અથવા દબાણનું માથું નાનું છે, જે ખોરાકની ક્ષમતા ઘટાડે છે.
3) ઘાટનું તાપમાન ઓછું છે, ઠંડકનો દર ઝડપી છે, અને ફીડિંગ ચેનલ અવરોધિત છે
3. નિવારક પગલાં:
1) કાસ્ટિંગ માળખું સુધારો અને હોટ સ્પોટ ઘટાડે છે
2) રાઈઝરને વ્યાજબી રીતે સેટ કરો, અથવા ફીડિંગ રીબ ઉમેરો કે જે પ્રક્રિયા પદ્ધતિઓ દ્વારા દૂર કરી શકાય છે, દબાણનું માથું વધારવું, જેથીરોકાણ કાસ્ટિંગચોક્કસ દબાણ હેડની ક્રિયા હેઠળ ક્રમિક રીતે મજબૂત કરી શકાય છે
3) ઠંડકનો દર ધીમો કરવા માટે રેડતા તાપમાન અને ઘાટનું તાપમાન યોગ્ય રીતે વધારવું
ગરમ ક્રેક
1. સમસ્યાનું વર્ણન:
સપાટી પર અથવા અંદર અનિયમિત ઇન્ટરગ્રેન્યુલર તિરાડો ઉત્પન્ન થાય છે, અને સપાટી ઓક્સિડાઇઝ્ડ થાય છે. તે ગંભીર રેતી સફાઈ પછી જોઈ શકાય છે, અને માત્ર હળવા પ્રક્રિયા અથવા ઘૂંસપેંઠ નિરીક્ષણ શોધી શકાય છે.
2. કારણો:
1) તે એલોયની રચના સાથે સંબંધિત છે, કાર્બન અને સિલિકોનની સામગ્રી વધારે છે, પ્રવાહી-ઘન તબક્કાની તાપમાન શ્રેણી મોટી છે, અને ગરમ ક્રેકીંગ સરળ છે
2) નીચા ઘાટનું તાપમાન, નબળી પીછેહઠ અને ઝડપી ઠંડક દર
3) કાસ્ટિંગની જાડાઈ મોટા પ્રમાણમાં બદલાય છે, અને સંક્રમણ ફીલેટ ખૂબ નાનું છે
3. નિવારક પગલાં:
1) એલોય અથવા સ્ટીલ્સ કે જે ગરમ તિરાડો માટે સંવેદનશીલ હોય છે, તેમના કાર્બન અને સિલિકોન સામગ્રીને શક્ય હોય ત્યાં સુધી મધ્યમ અને નીચલા મર્યાદા સુધી નિયંત્રિત કરવી જોઈએ.
2) રેડતી વખતે મોલ્ડનું તાપમાન વધારવું, કાસ્ટિંગના ઠંડકનો દર ધીમો કરો અથવા મોલ્ડ શેલની મજબૂતાઈ ઓછી કરો
3) કાસ્ટિંગ્સની જાડાઈના સાંધામાં એન્ટિ-ક્રેકીંગ પ્રક્રિયા પાંસળીઓ ઉમેરો અથવા ટ્રાન્ઝિશન ફીલેટ્સ વધારો
કોલ્ડ ક્રેક
નામ અને લાક્ષણિકતાઓ:
કાસ્ટિંગ પર સતત પેનિટ્રેટિંગ તિરાડો છે. અસ્થિભંગ પર ચળકતી સપાટી અથવા થોડી ઓક્સિડાઇઝ્ડ સપાટી દેખાય છે.
કારણો
1. કાસ્ટિંગની ઠંડકની પ્રક્રિયા દરમિયાન, સંકોચન અવરોધાય છે, જેના પરિણામે થર્મલ તણાવ અને તબક્કામાં ફેરફારનો તણાવ થાય છે, અને આ તણાવ સ્થિતિસ્થાપક સ્થિતિમાં સામગ્રીની મજબૂતાઈ કરતાં વધી જાય છે અને અસ્થિભંગનું કારણ બને છે.
2. શેલ સાફ કરવાની પ્રક્રિયામાં, ગેટ કાપવા, રાઇઝર અથવા એડજસ્ટિંગ દરમિયાન, શેષ તણાવ સાથે કાસ્ટિંગને અસ્થિભંગ થવા માટે બાહ્ય બળને આધિન કરવામાં આવે છે.
નિવારણ પદ્ધતિઓ
1. આકારની પીછેહઠક્ષમતા સુધારવા માટે ઠંડા તિરાડો પર સખત પાંસળી ઉમેરો, જેનાથી સંકોચન પ્રતિકાર અને કાસ્ટિંગ તણાવ ઘટે છે.
2. પોસ્ટ-કાસ્ટિંગ પ્રક્રિયામાં, કાસ્ટિંગ વચ્ચે ગંભીર અસર ટાળો.
બ્લોહોલ
નામ અને લાક્ષણિકતાઓ
કાસ્ટિંગ પર સરળ આંતરિક સપાટી સાથે સ્પષ્ટ અથવા અસ્પષ્ટ છિદ્રો છે.
કારણો
1. મોલ્ડ શેલની નબળી હવા અભેદ્યતા, જેના કારણે પોલાણમાં રહેલા ગેસને રેડતા સમયે ડિસ્ચાર્જ કરવામાં મોડું થાય છે.
2. શેલના આકારની અપૂરતી ફાયરિંગ, પરિણામે શેલ સામગ્રીમાં મોલ્ડ સામગ્રીના અવશેષો અને ગેસ ઉત્પન્ન કરતી સામગ્રીને અપૂરતી દૂર કરવામાં આવે છે.
3. ધાતુના પ્રવાહી ગેસનું પ્રમાણ ખૂબ વધારે છે, જેના કારણે નબળા ડિઓક્સિડેશન થાય છે.
4. રેડવાની સિસ્ટમની ગોઠવણી ગેરવાજબી છે, જેના કારણે માનવ ગેસ રેડવામાં સામેલ થાય છે.
નિવારણ પદ્ધતિઓ
1. શેલની હવાની અભેદ્યતામાં સુધારો કરો અને જો જરૂરી હોય તો વેન્ટ્સ ઉમેરો.
2. સંપૂર્ણપણે ફાયર શેલ.
3. ડીઓક્સિડેશન પદ્ધતિઓમાં સુધારો.
4. ગેટિંગ સિસ્ટમમાં સુધારો.
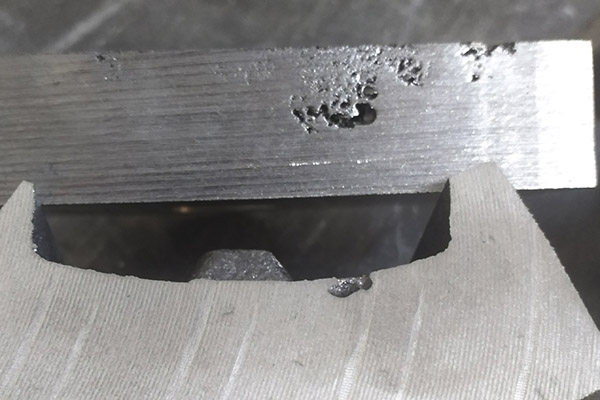
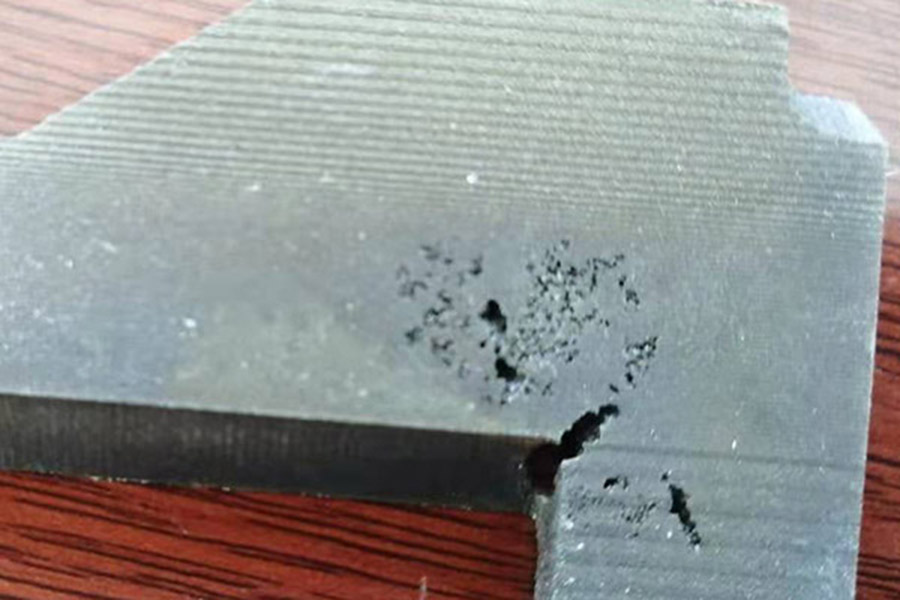
કાસ્ટિંગ પિટિંગ
નામ અને લાક્ષણિકતાઓ
કાસ્ટિંગની સપાટી પર ગાઢ બિંદુ જેવા ખાડાઓ છે.
કારણો
1. જ્યારે એથિલ સિલિકેટનો ઉપયોગ બાઈન્ડર તરીકે થાય છે, ત્યારે અપૂર્ણ હાઈડ્રોલાઈઝેટ કોટિંગ પ્રક્રિયામાં હોય છે, અંદરની સાપેક્ષ ભેજ ખૂબ ઓછી હોય છે, જેથી હાઈડ્રોલાઈઝેટને વધુ હાઈડ્રોલાઈઝ કરી શકાતું નથી, અને શેક્યા પછી "સફેદ હિમ" અવક્ષેપિત થાય છે.
2. જ્યારે પાણીના ગ્લાસનો ઉપયોગ બાઈન્ડર તરીકે કરવામાં આવે છે, ત્યારે મોલ્ડ શેલમાં રહેલું શેષ મીઠું પીગળેલી ધાતુ સાથે પ્રતિક્રિયા કરીને ખાડો બનાવે છે.
3. પીગળેલી ધાતુ નબળી રીતે ડીઓક્સિડાઇઝ્ડ છે અથવા ટેપીંગ દરમિયાન સ્લેગ સાફ કરવામાં આવતી નથી.
નિવારણ પદ્ધતિઓ:
1. બાઈન્ડર તરીકે એથિલ સિલિકેટનો ઉપયોગ કરતી વખતે, ઉમેરવામાં આવેલા પાણીના જથ્થાને યોગ્ય રીતે વધારવો અને શેષ અપૂર્ણ હાઇડ્રોલિસેટ્સને ઘટાડવા માટે પેઇન્ટ સ્ટુડિયોની સંબંધિત ભેજ વધારો.
2. બાઈન્ડર તરીકે પાણીના ગ્લાસનો ઉપયોગ કરતી વખતે, ડીવેક્સિંગ પછી શેલને એસિડિફાઇડ પાણીથી સાફ કરો.
3. સપાટીના કોટિંગને બાઈન્ડર તરીકે સિલિકા સોલમાં બદલો.
4. ગંધ દરમિયાન, ડિઓક્સિડેશન અને સ્લેગ દૂર કરવાને મજબૂત કરો.
કાસ્ટિંગ સબક્યુટેનીયસ પિનહોલ
નામ અને લાક્ષણિકતાઓ
કાસ્ટિંગની સપાટીને પોલિશ કર્યા પછી, નાના કાળા ફોલ્લીઓ દેખાય છે. આ ઘટના મોટે ભાગે થાય છેનિકલ-ક્રોમિયમ સ્ટેનલેસ સ્ટીl.
કારણો:
1. ધાતુના પીગળેલા સમયે ખૂબ જ રિસાયકલ કરેલ સામગ્રીનો ઉપયોગ કરવામાં આવે છે, અથવા રિસાયકલ કરેલ સામગ્રીને યોગ્ય રીતે સારવાર આપવામાં આવી નથી.
2. ગલન પ્રક્રિયા દરમિયાન, પીગળેલી ધાતુનું ઓક્સિડેશન થાય છે અથવા પીગળેલી ધાતુ ગેસને શોષી લે છે, પરિણામે અપૂરતું ડીઓક્સિડેશન થાય છે.
3. શેલ સામગ્રીની અશુદ્ધતા સામગ્રી ખૂબ વધારે છે, અથવા બોન્ડિંગ એજન્ટ અને પીગળેલી ધાતુની રાસાયણિક પ્રતિક્રિયા છે.4. ગેટિંગ સિસ્ટમની ગેરવાજબી સેટિંગ.
નિવારણ પદ્ધતિઓ:
1. રિસાયકલ કરેલ સામગ્રીની માત્રાને નિયંત્રિત કરો અથવા ઘટાડો કરો, અને રેતી ફૂંકાયા અથવા શોટ બ્લાસ્ટિંગ પછી રિસાયકલ કરેલ સામગ્રીનો ઉપયોગ કરવાની જરૂર છે.
2. સ્મેલ્ટિંગ પ્રક્રિયાને સખત રીતે નિયંત્રિત કરો અને ડિઓક્સિડેશનને મજબૂત કરો.
3. ફ્યુઝ્ડ કોરન્ડમ, ઝિર્કોન રેતી અને સિલિકા સોલ અથવા એથિલ સિલિકેટ પેઇન્ટનો ઉપયોગ કરો.
4. રેડવાની અને વેન્ટ હોલ્સ વધારવા માટે બોટમ ઈન્જેક્શન પદ્ધતિનો ઉપયોગ કરવાનો પ્રયાસ કરો.
સ્ટીકી રેતી
નામ અને લાક્ષણિકતાઓ
રનરની નજીક અથવા કાસ્ટિંગની અંદર એક ચીકણું રેતીનું સ્તર છે, અને રેતી ફૂંકાયા પછી ત્યાં ઉછરેલા બૂર્સ અથવા ખાડાઓ છે.
કારણો
1. કોટિંગ સપાટીના સ્તરમાં વપરાતા પ્રત્યાવર્તન પાવડરની અશુદ્ધતાનું પ્રમાણ ખૂબ વધારે છે અને આ અશુદ્ધિઓ પીગળેલી ધાતુ સાથે પ્રતિક્રિયા કરીને નીચા ગલનબિંદુ યુટેક્ટિક બનાવે છે.
2. રેડવાનું તાપમાન ખૂબ ઊંચું છે, ખાસ કરીને સ્ટીલ ગ્રેડ જેમાં Al, Ti અને અન્ય તત્વો હોય છે, જે પીગળેલી ધાતુ અને સિલિકા વચ્ચે રાસાયણિક પ્રતિક્રિયાનું કારણ બને છે.
3. ગેટીંગ સિસ્ટમની ગોઠવણી ગેરવાજબી છે, અને આંતરિક રનરમાંથી મોટી માત્રામાં પીગળેલી ધાતુ વહે છે, જે સ્થાનિક ઓવરહિટીંગનું કારણ બને છે.
નિવારણ પદ્ધતિઓ
1. સિલિકા રેતીને બદલે ફ્યુઝ્ડ સ્ટીલ જેડ અથવા ઝિર્કોન રેતીનો ઉપયોગ કરો, અને બાઈન્ડર તરીકે પાણીના ગ્લાસનો ઉપયોગ ન કરવાનો પ્રયાસ કરો.
2. રેડતા તાપમાનને યોગ્ય રીતે ઓછું કરો.
3. ગરમીનું સંતુલન સમાયોજિત કરવા અને સ્થાનિક ઓવરહિટીંગ ઘટાડવા માટે આંતરિક દોડવીર ઉમેરો.
ડિલેટન્ટ
નામ અને લાક્ષણિકતાઓ
કાસ્ટિંગના મોટા પ્લેન પર સ્થાનિક સોજો, બાઈન્ડર તરીકે પાણીના ગ્લાસનો ઉપયોગ કરતી વખતે આ ઘટના વધુ સ્પષ્ટ છે.
કારણો
1. કાસ્ટિંગ માળખું ગેરવાજબી છે અને પ્લેન વિસ્તાર ખૂબ મોટો છે.
2. ઊંચા તાપમાને શેલમાં નીચી તાકાત હોય છે અને તે પીગળેલા ધાતુના દબાણનો સામનો કરી શકતો નથી.
નિવારણ પદ્ધતિઓ
1. માળખું સુધારો, પ્રક્રિયા પાંસળી ઉમેરો અથવા પ્લેન પર પ્રક્રિયા છિદ્રો.
2. શેલ બનાવતી વખતે, ઓછી અશુદ્ધિઓ અને ઉચ્ચ પ્રત્યાવર્તન સાથે શેલ સામગ્રીનો ઉપયોગ કરો અથવા શેલની જાડાઈ વધારો.
સ્લેગ
નામ અને લાક્ષણિકતાઓ
કાસ્ટિંગની અંદર અથવા સપાટી પર સ્લેગ અથવા અન્ય ભંગાર છે. એક્સ-રે અથવા ચુંબકીય નિરીક્ષણ દ્વારા આંતરિક સમાવેશને શોધવાની જરૂર છે.
કારણો
1. સ્લેગ સામગ્રી ખૂબ પાતળી છે અને ટેપ કરતા પહેલા સાફ કરવામાં આવતી નથી.
2. ક્રુસિબલના ટેપીંગ ટ્રફ પરનો કાટમાળ ટેપ કરતા પહેલા સાફ કરવામાં આવ્યો ન હતો અને તેને પીગળેલી ધાતુમાં લાવવામાં આવ્યો હતો.
3. કાસ્ટ કરતી વખતે, સ્લેગ રીટેન્શન સારી નથી, અને સ્લેગ પીગળેલી ધાતુ સાથે પોલાણમાં પ્રવેશ કરે છે.
નિવારણ પદ્ધતિઓ
1. સ્લેગ સામગ્રીની સ્નિગ્ધતા વધારવા અને સ્લેગને દૂર કરવાનું સરળ બનાવવા માટે ટેપ કરતા પહેલા સ્લેગ સામગ્રીની રચનાને સમાયોજિત કરો.
2. લાડુમાં પીગળેલી ધાતુમાં અશુદ્ધિઓ લાવવાનું ટાળવા માટે સ્ટીલના આગળના ચાટમાં રહેલા કાટમાળને સાફ કરો.
3. કાસ્ટિંગ પહેલાં, પીગળેલાકાસ્ટ તેલસ્લેગ ફ્લોટિંગની સુવિધા માટે યોગ્ય રીતે શાંત થવું જોઈએ.
4. સ્લેગ સ્ટોપર અથવા સિરામિક ફિલ્ટર વડે ચાની કીટલી રેડતા લાડુ લો.
ડીકાર્બ્યુરાઇઝેશન
નામ અને લક્ષણો
કાસ્ટિંગની સપાટીના સ્તરની કાર્બન સામગ્રી મેટ્રિક્સ કરતા ઓછી છે.
કારણો
1. કાસ્ટિંગ દરમિયાન, પીગળેલી ધાતુ અને ઘાટનું તાપમાન ઊંચું હોય છે, અને કાસ્ટિંગનો ઘનકરણ દર ધીમો હોય છે.
2. ડીકાર્બ્યુરાઇઝેશન લેયરની ઊંડાઈ કાસ્ટિંગના ઠંડકના વાતાવરણના વાતાવરણ સાથે સંબંધિત છે. ઓક્સિડાઇઝિંગ વાતાવરણની સાંદ્રતા જેટલી વધારે છે, ડીકાર્બ્યુરાઇઝેશન વધુ ગંભીર.
નિવારણ પદ્ધતિઓ
1. ઠંડકના દરને ઝડપી બનાવવા માટે કાસ્ટિંગ તાપમાન અને ઘાટનું તાપમાન યોગ્ય રીતે ઘટાડે છે.
2. કૃત્રિમ રીતે ઘાટની આસપાસ ઘટાડાનું વાતાવરણ બનાવો, જેમ કે ઘાટમાં બેરિયમ કાર્બોનેટ અને ચારકોલ પાવડર ઉમેરવા.
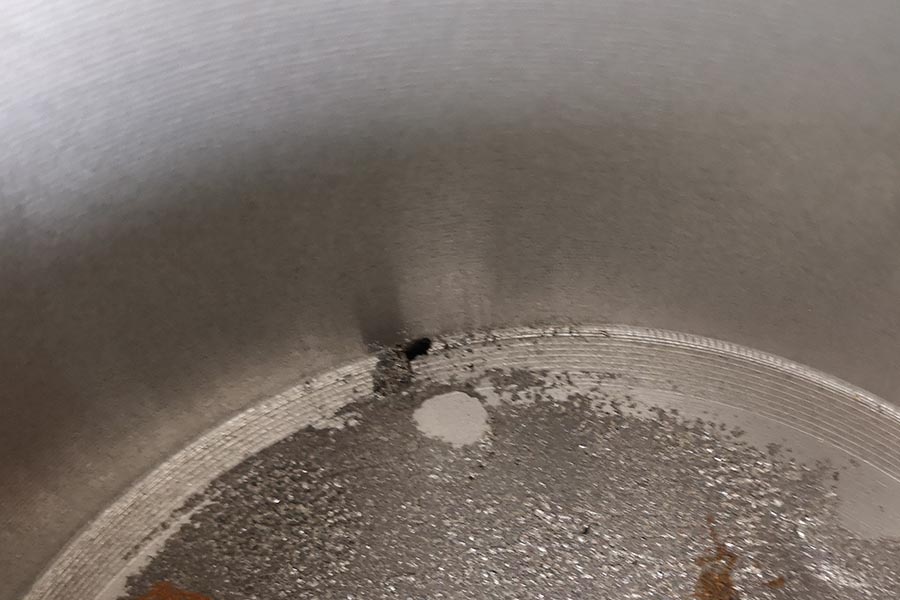
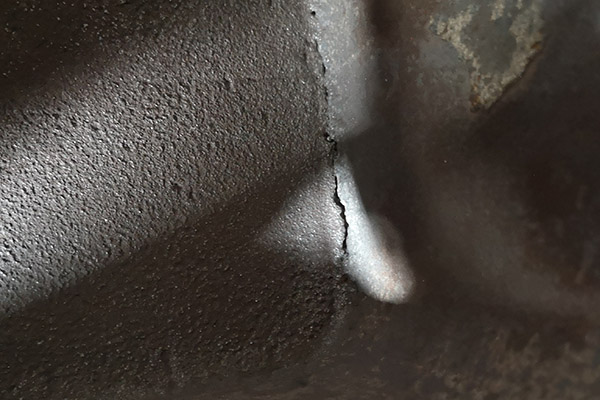
પોસ્ટ સમય: જાન્યુઆરી-22-2021